Come progettare parti in plastica
Breve descrizione:
Per progettare parti in plasticaè definire la forma, le dimensioni e la precisione delle parti, in base al ruolo che le parti giocano nel prodotto, e alla regola del processo di stampaggio della plastica. Il risultato finale sono i disegni per la fabbricazione dello stampo e della parte in plastica.
La produzione del prodotto inizia con il design. La progettazione delle parti in plastica determina direttamente la realizzazione della struttura interna, il costo e la funzione del prodotto, e determina anche la fase successiva della produzione dello stampo, il costo e il ciclo, nonché il processo e il costo di stampaggio a iniezione e post-elaborazione.
Le parti in plastica sono ampiamente utilizzate in vari prodotti, strutture e vite delle persone nella società moderna. Le parti in plastica richiedono forme e funzioni diverse. Usano materiali plastici e le loro proprietà sono molteplici. Allo stesso tempo, ci sono molti modi per realizzare parti in plastica nell'industria. Quindi progettare parti in plastica non è un lavoro semplice.
Il design e il materiale di parti diverse vengono prodotti con lavorazioni diverse. La lavorazione per lo stampaggio della plastica comprende principalmente di seguito:
1. stampaggio a iniezione
Stampaggio 2.blowing
Stampaggio 3.compression
Stampaggio 4.rotational
5.termoformatura
6.estrusione
7.fabbricazione
8. schiuma
Esistono numerosi modi per produrli in serie. Lo stampaggio a iniezione è un metodo di produzione popolare, poiché le parti in plastica stampate a iniezione dal 50% al 60% sono prodotte dallo stampaggio a iniezione, è una capacità di produzione ad alta velocità.
Vetrina per alcune parti in plastica che abbiamo progettato:
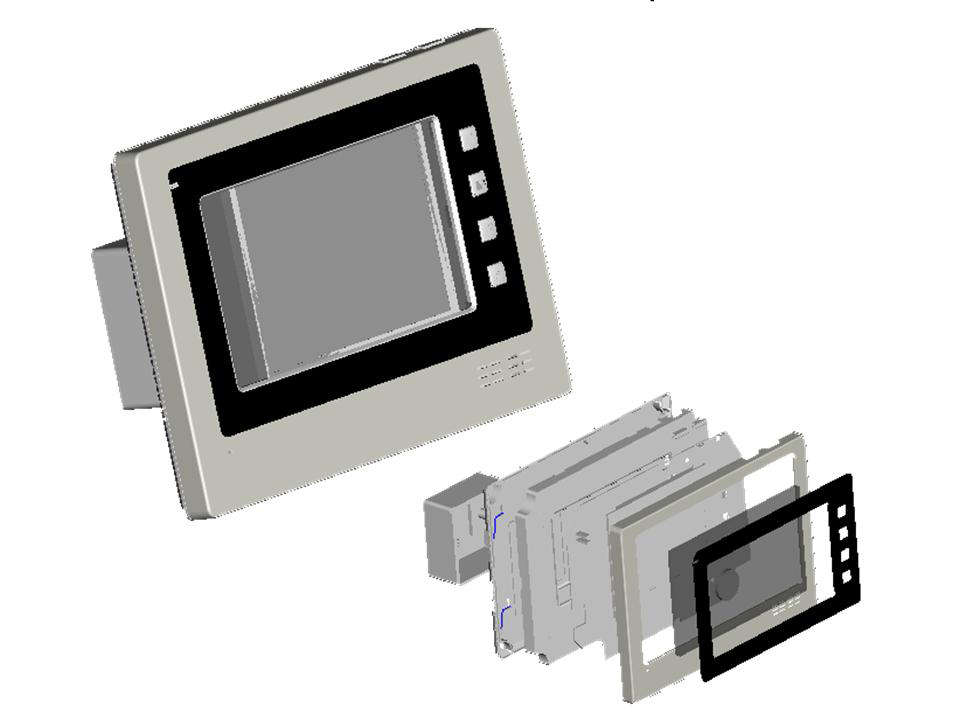
Custodia in plastica del telefono per visione
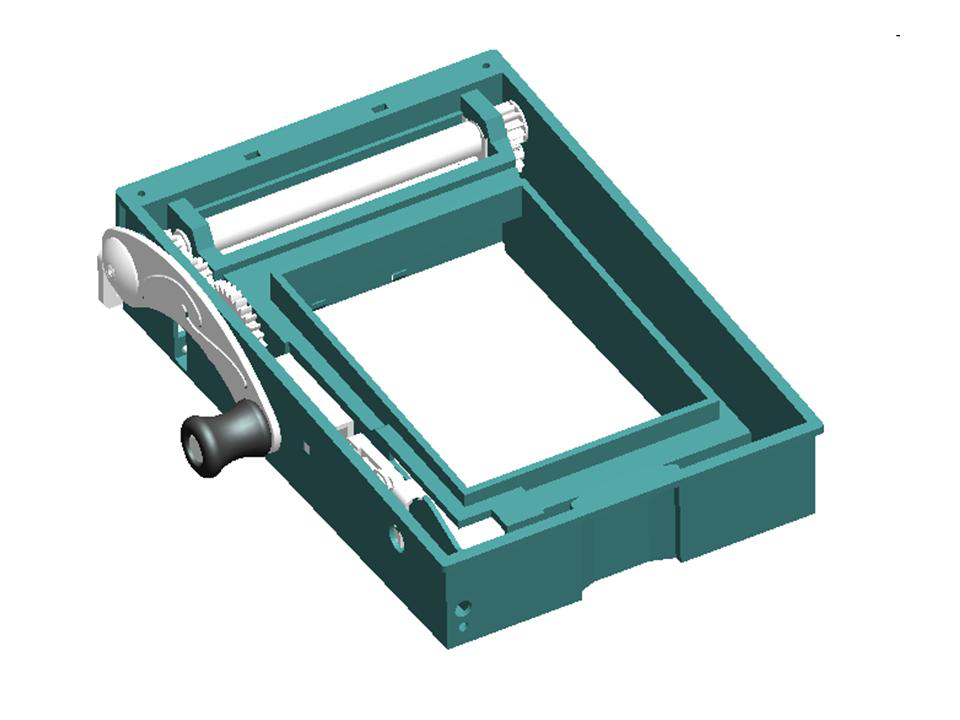
Parti in plastica del meccanismo
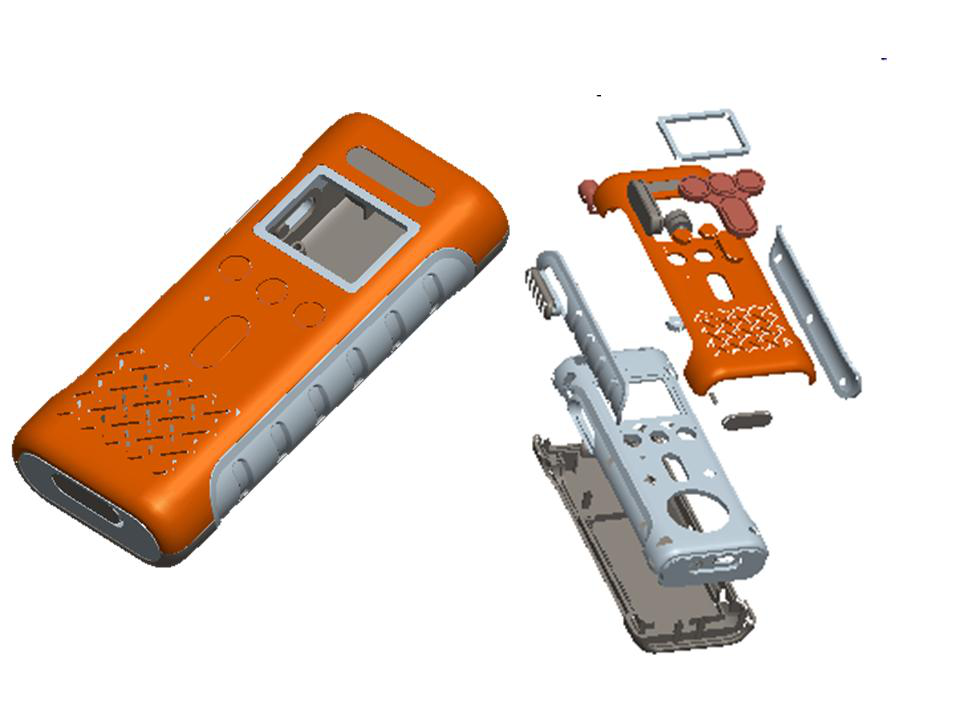
Custodie in plastica di elettronica
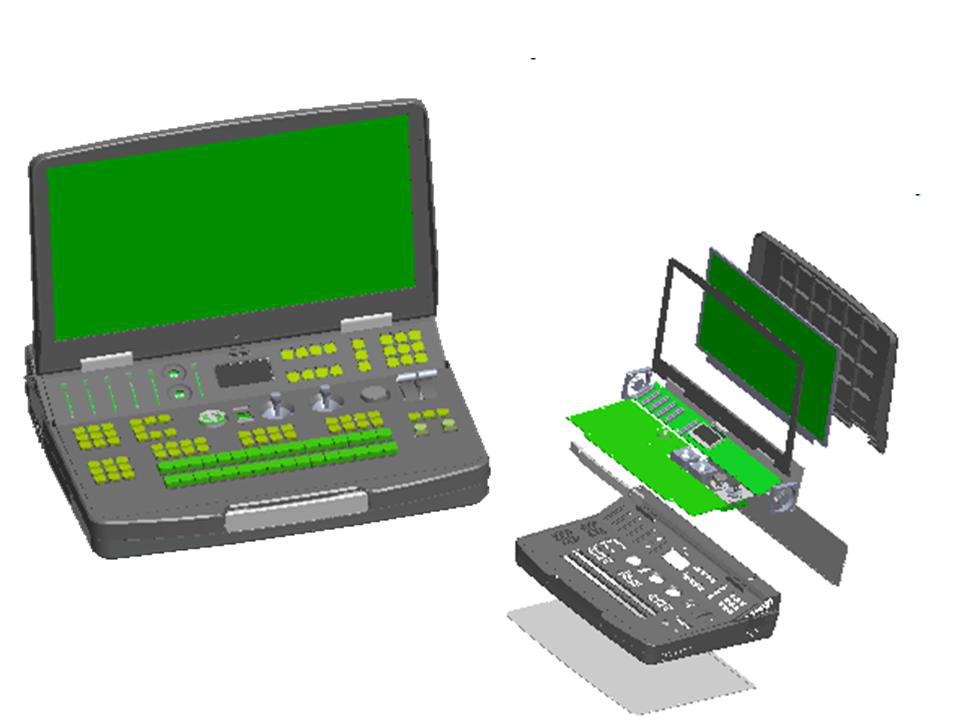
Custodia in plastica per strumento
Di seguito condividiamo i dettagli su come progettare parti in plastica in tre aspetti
* 10 suggerimenti per progettare parti in plastica che devi conoscere
1.Determinare l'aspetto del design e le dimensioni del prodotto.
Questo è il primo passo dell'intero processo di progettazione. In base alle ricerche di mercato e ai requisiti dei clienti, determinare l'aspetto e la funzione dei prodotti e formulare attività di sviluppo del prodotto.
In base all'attività di sviluppo, il team di sviluppo esegue l'analisi di fattibilità tecnica e tecnologica del prodotto e costruisce il modello di aspetto 3D del prodotto. Quindi, in base alla realizzazione della funzione e all'assemblaggio del prodotto, vengono pianificate le parti possibili.
2. Separare le singole parti dai disegni del prodotto, scegliere il tipo di resina plastica per le parti in plastica
Questo passaggio consiste nel separare le parti dal modello 3D ottenuto nel passaggio precedente e progettarle come singole. In base ai requisiti funzionali delle parti, scegliere materie prime plastiche o materiali hardware adatti. Ad esempio, l'ABS viene solitamente utilizzato in
shell, ABS / BC o PC devono avere determinate proprietà meccaniche, parti trasparenti come paralume, lampione in PMMA o PC, ingranaggi o parti soggette ad usura POM o nylon.
Dopo aver selezionato il materiale delle parti, è possibile avviare la progettazione dettagliata.
3. Definire gli angoli di sformo
Gli angoli di sformo consentono la rimozione della plastica dallo stampo. Senza angoli di sformo, la parte offrirebbe una resistenza significativa a causa dell'attrito durante la rimozione. Gli angoli di sformo dovrebbero essere presenti all'interno e all'esterno della parte. Più profonda è la parte, maggiore è l'angolo di sformo. Una semplice regola pratica è avere un angolo di sformo di 1 grado per pollice. Non avere un angolo di sformo sufficiente può provocare graffi lungo i lati della parte e / o segni di grandi dimensioni del perno di espulsione (ne parleremo più avanti).
Angoli di sformo della superficie esterna: più profonda è la parte, maggiore è l'angolo di sformo. Una semplice regola pratica è avere un angolo di sformo di 1 grado per pollice. Non avere un angolo di sformo sufficiente può provocare graffi lungo i lati della parte e / o segni di grandi dimensioni del perno di espulsione (ne parleremo più avanti).
Di solito, per avere una superficie di bell'aspetto, la trama viene realizzata sulla superficie delle parti. Il muro con la trama è ruvido, l'attrito è grande e non è facile rimuoverlo dalla cavità, quindi richiede un angolo di disegno maggiore. La consistenza più grossolana è, l'angolo di sformo più grande necessario.
4. Definire lo spessore della parete / spessore uniforme
Lo stampaggio a forma solida non è desiderato nello stampaggio a iniezione per i seguenti motivi:
1) .Il tempo di raffreddamento è proporzionale al quadrato dello spessore della parete. Il lungo tempo di raffreddamento del solido sconfiggerà l'economia della produzione di massa. (cattivo conduttore di calore)
2) .La sezione più spessa si restringe più della sezione più sottile, quindi introduce un restringimento differenziale con conseguente deformazione o segni di affondamento, ecc. (Caratteristiche di restringimento della plastica e caratteristiche di pvT)
Pertanto abbiamo una regola di base per la progettazione di parti in plastica; per quanto possibile, lo spessore della parete deve essere uniforme o costante per tutta la parte. Questo spessore della parete è chiamato spessore nominale della parete.
Se c'è una sezione solida nella parte, dovrebbe essere resa cava introducendo l'anima. Ciò dovrebbe garantire uno spessore della parete uniforme attorno al nucleo.
3) Quali sono le considerazioni per decidere lo spessore della parete?
Deve essere abbastanza spesso e rigido per il lavoro. Lo spessore della parete potrebbe essere compreso tra 0,5 e 5 mm.
Deve anche essere abbastanza sottile da raffreddarsi più velocemente, con conseguente minor peso delle parti e maggiore produttività.
Qualsiasi variazione nello spessore della parete deve essere mantenuta il più possibile ridotta.
Una parte in plastica con pareti di spessore variabile subirà velocità di raffreddamento e ritiri differenti. In tal caso, ottenere una stretta tolleranza diventa molto difficile e molte volte impossibile. Dove la variazione dello spessore della parete è essenziale, la transizione tra i due dovrebbe essere graduale.
5.Progettazione della connessione tra le parti
Di solito abbiamo bisogno di collegare due shell insieme. Per formare una stanza chiusa tra di loro per posizionare i componenti interni (assemblaggio PCB o meccanismo).
I soliti tipi di connessione:
1). Moschettoni:
La connessione con moschettoni è comunemente utilizzata nei prodotti di piccole e medie dimensioni. La sua caratteristica è che i moschettoni sono generalmente posizionati sul bordo delle parti e la dimensione del prodotto può essere ridotta. Una volta assemblato, viene chiuso direttamente senza l'utilizzo di strumenti come cacciaviti, stampi per saldatura a ultrasuoni e altri. Lo svantaggio è che i moschettoni possono causare muffe più complicate. Il meccanismo di scorrimento e il meccanismo di sollevamento sono necessari per realizzare il collegamento dei moschettoni e aumentare il costo dello stampo.
2). Giunti a vite:
I giunti a vite sono solidi e affidabili. In particolare, il fissaggio vite + dado è molto affidabile e durevole, consentendo smontaggi multipli senza crepe. Il collegamento a vite è adatto per prodotti con grande forza di bloccaggio e smontaggio multiplo. Lo svantaggio è che la colonna della vite occupa più spazio.
3). Borchie di montaggio:
La connessione delle borchie di montaggio serve a fissare due parti mediante la stretta coordinazione tra le borchie e i fori. Questo modo di connessione non è abbastanza forte da consentire lo smontaggio dei prodotti. Lo svantaggio è che la forza di bloccaggio diminuirà con l'aumentare del tempo di smontaggio.
4). Saldatura a ultrasuoni:
La saldatura a ultrasuoni consiste nel mettere le due parti nello stampo ad ultrasuoni e fondendo la superficie di contatto sotto l'azione della saldatrice ad ultrasuoni. La dimensione del prodotto può essere inferiore, lo stampo a iniezione è relativamente semplice e la connessione è stabile. Lo svantaggio è l'uso di stampi ad ultrasuoni e saldatrici ad ultrasuoni, la dimensione del prodotto non può essere troppo grande. Dopo lo smontaggio, le parti ad ultrasuoni non possono essere riutilizzate.
6. Sottosquadri
I sottosquadri sono elementi che interferiscono con la rimozione di una delle metà dello stampo. I sottosquadri possono apparire praticamente ovunque nel disegno. Questi sono altrettanto inaccettabili, se non peggiori, della mancanza di un angolo di sformo da parte. Tuttavia, alcuni sottosquadri sono necessari e / o inevitabili. In quei casi, necessario
i sottosquadri sono prodotti facendo scorrere / muovendo parti nello stampo.
Tieni presente che la creazione di sottosquadri è più costosa quando si produce lo stampo e dovrebbe essere ridotta al minimo.
7.Supporto Nervature / Fazzoletti
Le nervature nella parte in plastica migliorano la rigidità (rapporto tra carico e flessione della parte) della parte e ne aumentano la rigidità. Migliora anche la capacità di muffa poiché accelerano il flusso di fusione nella direzione della nervatura.
Le nervature vengono posizionate lungo la direzione di massima sollecitazione e deflessione sulle superfici non in aspetto della parte. Anche il riempimento, il restringimento e l'espulsione dello stampo dovrebbero influenzare le decisioni di posizionamento delle costole.
Le costole che non si uniscono alla parete verticale non dovrebbero terminare bruscamente. Il passaggio graduale alla parete nominale dovrebbe ridurre il rischio di concentrazione dello stress.
Rib - dimensioni
Le costole dovrebbero avere le seguenti dimensioni.
Lo spessore delle nervature deve essere compreso tra 0,5 e 0,6 volte lo spessore nominale della parete per evitare segni di affondamento.
L'altezza delle nervature dovrebbe essere da 2,5 a 3 volte lo spessore nominale della parete.
La nervatura dovrebbe avere un angolo di sformo da 0,5 a 1,5 gradi per facilitare l'espulsione.
La base della nervatura deve avere un raggio da 0,25 a 0,4 volte lo spessore nominale della parete.
La distanza tra due nervature dovrebbe essere da 2 a 3 volte (o più) lo spessore nominale della parete.
8.Bordi irradiati
Quando due superfici si incontrano, forma un angolo. All'angolo, lo spessore della parete aumenta fino a 1,4 volte lo spessore nominale della parete. Ciò si traduce in un restringimento differenziale e uno stress incorporato e un tempo di raffreddamento più lungo. Pertanto, il rischio di guasto nel servizio aumenta negli angoli acuti.
Per risolvere questo problema, gli angoli dovrebbero essere levigati con il raggio. Il raggio dovrebbe essere fornito sia esternamente che internamente. Non avere mai angoli interni affilati in quanto favoriscono la crepa. Il raggio dovrebbe essere tale da confermare la regola dello spessore della parete costante. È preferibile avere un raggio da 0,6 a 0,75 volte lo spessore della parete agli angoli. Non avere mai angoli interni affilati in quanto favoriscono la crepa.
9.Screw boss design
Usiamo sempre viti per fissare insieme due metà custodie o fissare PCBA o altri componenti sulle parti in plastica. Quindi i boss delle viti sono la struttura per l'avvitamento e le parti fisse.
La borchia della vite è di forma cilindrica. Il boss può essere collegato alla base con la parte madre o può essere collegato a lato. Il collegamento laterale può provocare una sezione spessa di plastica, il che non è desiderabile in quanto può causare segni di affondamento e aumentare il tempo di raffreddamento. Questo problema può essere risolto collegando la borchia attraverso una nervatura alla parete laterale come mostrato nello schizzo. La sporgenza può essere resa rigida fornendo nervature di sostegno.
La vite viene utilizzata sulla borchia per fissare qualche altra parte. Esistono tipi di viti filettate e viti per taglio battistrada. Le viti autoformanti vengono utilizzate sui materiali termoplastici e le viti autofilettanti vengono utilizzate sulle parti in plastica termoindurente anelastica.
Le viti autofilettanti producono filettature femmina sulla parete interna della borchia mediante flusso freddo - la plastica viene deformata localmente anziché tagliata.
La borchia della vite deve avere dimensioni adeguate per resistere alle forze di inserimento della vite e al carico posto sulla vite in servizio.
La dimensione del foro rispetto alla vite è fondamentale per la resistenza allo strappo del filetto e all'estrazione della vite.
Il diametro esterno della borchia dovrebbe essere abbastanza grande da resistere alle sollecitazioni del telaio dovute alla formazione del filo.
Il foro ha un diametro leggermente maggiore nella cavità di ingresso per una breve lunghezza. Questo aiuta a localizzare la vite prima di inserirla. Riduce anche le sollecitazioni all'estremità aperta della borchia.
I produttori di polimeri forniscono linee guida per determinare la dimensione della sporgenza per i loro materiali. I produttori di viti forniscono anche linee guida per la corretta dimensione del foro per la vite.
È necessario prestare attenzione per garantire giunti saldati robusti attorno al foro della vite nella sporgenza.
Bisogna fare attenzione per evitare lo stress modellato nel capo in quanto può fallire in un ambiente aggressivo.
Il foro nella borchia dovrebbe essere più profondo della profondità della filettatura.
10.Decorazione della superficie
A volte, per ottenere un bell'aspetto, spesso eseguiamo un trattamento speciale sulla superficie della custodia in plastica.
Come: struttura, alta lucentezza, verniciatura a spruzzo, incisione laser, stampa a caldo, galvanica e così via. È necessario tenerne conto nella progettazione del prodotto in anticipo, per evitare che le successive lavorazioni non possano essere ottenute o che cambiamenti di dimensioni influenzino l'assemblaggio del prodotto.